Technical textiles are rapidly transforming the automotive landscape—not only redefining performance but also advancing sustainability across the industry. What once served limited roles in seat belts and airbags now powers a revolution in vehicle design and engineering. These advanced materials are embedded across the entire spectrum of modern mobility—spanning lightweight composites for body panels, acoustic insulation, thermal regulation fabrics, and intelligent textiles integrated with sensors.
As the automotive sector accelerates toward electrification and enhanced fuel efficiency, the demand for robust, lightweight, and high-performance materials has surged. Technical textiles rise to the occasion. They slash vehicle weight without sacrificing structural integrity or passenger safety, directly boosting energy efficiency and curbing emissions.
Meanwhile, breakthroughs in biodegradable materials, recycled fiber integration, and nanotechnology-infused fabrics are positioning technical textiles at the heart of sustainable automotive manufacturing. These innovations not only support global environmental goals but also elevate the driving experience—delivering UV resistance, antimicrobial surfaces, and advanced fire-retardant capabilities.
Looking ahead, the role of technical textiles will grow even more sophisticated. With autonomous vehicles and smart interiors on the horizon, these materials will shift from passive components to active enablers—adapting dynamically to enhance user interaction and comfort. Simply put, technical textiles are no longer just supporting the automotive industry; they are steering it toward a smarter, greener, and more resilient future.
In an exclusive conversation with The Interview World during the Conference on The Future of Textiles – Challenges and Opportunities in Man-Made Fibres, organized by the PHD Chamber of Commerce and Industry (PHDCCI), Sanjay Sharma—President and Chief Operating Officer of BMD Private Limited—offers compelling insights. He unpacks the evolution of India’s textile sector, explores the technological advancements and resources vital for scaling up technical textiles, and highlights the immense potential within carbon textile innovation. Here are the most striking takeaways from his forward-looking dialogue.
Q: How is the Indian textile industry evolving in recent years, and what are the key challenges it continues to face?
A: The Indian textile industry is experiencing robust growth, contributing approximately 2.7% to the nation’s GDP and employing around 45 million people. Moreover, it accounts for nearly 4% of global trade—a significant footprint on the world stage.
However, the industry faces several critical challenges. Chief among them are the inconsistent availability of quality raw materials, mounting environmental concerns, and the urgent need for sustainable practices. Compounding these issues is the declining demand in Western markets, coupled with the erosion of traditional skills and a growing shortage of skilled manpower.
Looking ahead, the future lies in the development and adoption of technical textiles. To remain competitive, the industry must embrace best practices, invest in eco-friendly and sustainable materials, and, most importantly, prioritize skill development across the value chain. The path forward demands innovation, agility, and a renewed commitment to excellence.
Q: In the context of technical textiles, what types of resources and technologies are essential to effectively scale this sector in India?
A: Absolutely. When we talk about technical textiles, especially in the automotive and mobile tech industries, the focus shifts sharply to performance-driven materials. These sectors demand raw materials with high tenacity and exceptional strength—qualities essential for durability and safety.
In particular, micro yarns are gaining prominence due to their superior functionality. Technical textiles, by nature, serve two distinct purposes: aesthetics and functionality. However, in high-performance applications, functionality unquestionably takes precedence over appearance.
To meet these demands, manufacturers must ensure the use of high-quality raw materials, advanced machinery, and—most critically—robust process systems. Without the right manufacturing protocols and infrastructure, even the best materials fall short. In short, success in this space hinges on precision, innovation, and strict adherence to best practices.
Q: What is the growth potential of technical textiles, and which industries represent the key areas of application and demand?
A: In the realm of technical textiles, particularly within mobility space, their applications span a wide range—airlines, railways, automobiles, trucks, and caravans. These materials are integral to the modern transportation ecosystem.
Notably, the automotive industry has emerged as a major growth driver. India, for instance, has consistently recorded an impressive growth rate of approximately 11% over the past 10 to 15 years. This sustained momentum has significantly boosted the demand for technical textiles.
Each car, on average, consumes nearly 40 kilograms of textile materials. These include everything from tire cord yarn and Nylon 6,6 to airbag fabrics, seat belts, seat covers, roof lining, insulation fabrics, and specialized filter fabrics.
Clearly, as automotive innovation accelerates, the role of technical textiles becomes not just relevant—but indispensable.
Q: What major advancements are shaping the carbon textile sector, and how is India positioned in terms of research, development, and commercialization?
A: Until now, carbon composites have played a vital role across several high-performance sectors. They are extensively used in wind turbines and aircraft, thanks to their exceptional strength-to-weight ratio.
Today, with the global shift toward electric vehicles, the automotive industry has intensified its focus on weight reduction to improve efficiency and range. In this context, carbon fibre has emerged as a crucial alternative to traditional steel. Components such as bumpers, boots, doors, and structural panels are increasingly being designed with lightweight carbon composites to meet these evolving demands.
However, India currently lacks domestic manufacturing capabilities for these advanced materials. As a result, the industry remains heavily reliant on imports, highlighting a significant gap—and an urgent opportunity—for investment in indigenous production.
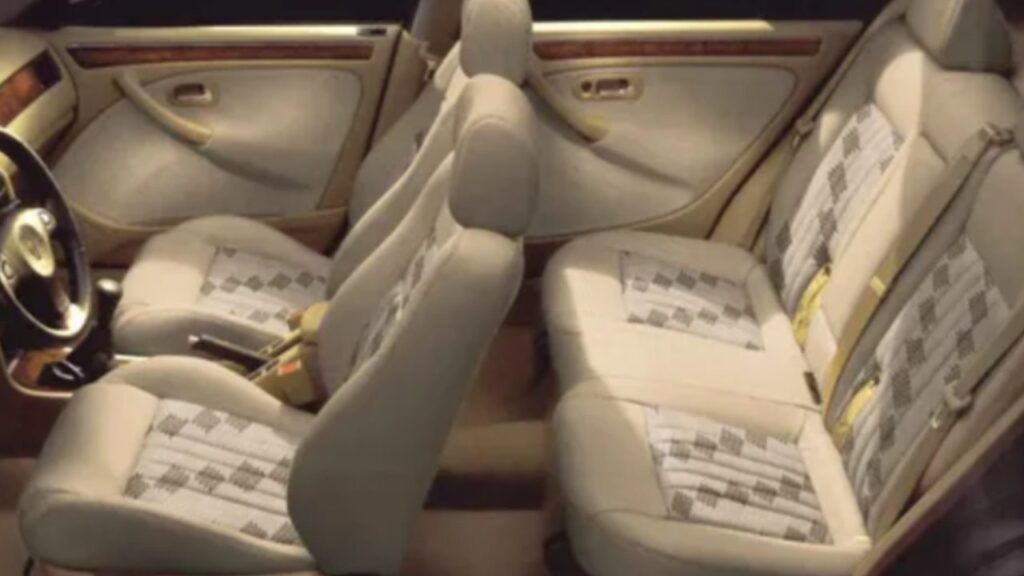