Renishaw plc, a global powerhouse in engineering technologies, operates from its headquarters in Wotton-under-Edge, Gloucestershire, UK. Established in 1973 by Sir David McMurtry and John Deer, the company has forged a stellar legacy by revolutionizing precision measurement and process control—enabling seamless automation across industries.
Renishaw’s diverse portfolio includes coordinate-measuring machines, machine tool probes, calibration systems, encoders, metal additive manufacturing platforms, and advanced healthcare technologies such as Raman spectroscopy and neurosurgical instruments. These solutions power mission-critical sectors like aerospace, automotive, electronics, energy, and life sciences.
What truly sets Renishaw apart is its uncompromising focus on innovation. Each year, it reinvests 13% to 18% of its revenue into research and development—an unwavering commitment that continually places the company at the forefront of manufacturing technology. This strategic reinvestment fuels breakthroughs in precision, efficiency, and digital manufacturing capabilities.
In India, Renishaw has established a formidable footprint across industrial hotspots including Bangalore, Pune, Delhi, Chennai, and Vadodara. Through these hubs, it actively propels India’s manufacturing landscape with cutting-edge metrology solutions and automation tools tailored for high-performance industries.
Renishaw’s enduring legacy is rooted in engineering excellence, pioneering spirit, and a forward-looking approach to transforming global manufacturing.
At the 5th AeroDef India Manufacturing Exhibition & Conference, The Interview World engaged in an exclusive conversation with Rahul Desale, Marketing & Communication Manager at Renishaw Metrology Systems Limited. Desale shed light on how Renishaw integrates precision into industrial automation, explained how its technologies detect production defects, and shared his outlook on India’s growing demand for automation tools. He also offered a glimpse into the company’s innovation roadmap over the next five to ten years.
Here are the key insights from that illuminating discussion.
Q: How is Renishaw leveraging its precision technologies to enhance industrial automation processes?
A: Renishaw brings over five decades of engineering excellence, with roots deeply embedded in aerospace innovation. The company’s journey began when our late co-founder, Sir David McMurtry, faced a critical inspection challenge while working at Rolls-Royce on a Concorde engine. In solving that problem, he invented the first touch-trigger probe—laying the foundation for a legacy in precision measurement.
Today, our probing systems lie at the heart of automated CNC machining, delivering unmatched accuracy. This is why we champion the ethos: Automation for Everyone.
At Renishaw, we believe automation must be universal—accessible to manufacturers of every scale. Our solutions are built on a simple yet powerful principle: anything that’s cut must be measured. Through a blend of advanced sensors, automated workflows, and ultra-precise measurement systems, we empower manufacturers to produce high-quality parts at speed.
Our probing systems play a critical role. They automate tool setting, detect tool breakage, and ensure correct part positioning—significantly reducing reliance on manual labor. As pioneers in this space, we continue to innovate machine tool solutions that redefine shop floor efficiency.
Among our standout technologies is the Equator™ gauging system—a revolutionary shop-floor comparator. It delivers high repeatability and remains thermally stable, even in extreme environments like India, where summer temperatures regularly soar above 40°C. Designed for real-world manufacturing conditions, the Equator™ system enables 100% part inspection and provides real-time process feedback. Integrated with CNC machines, it facilitates immediate in-process corrections—ensuring consistent quality at the source.
Another core offering is our suite of encoders for position and motion control feedback. Built for versatility, Renishaw encoders are embedded across industries—from electric vehicles and drones to gimbals, printing systems, and high-precision CNC machines. Wherever accurate position feedback is critical, our encoders deliver.
That’s why we’re here at this exhibition—demonstrating solutions trusted by manufacturers for over 50 years. With each innovation, we help thousands of companies worldwide streamline their operations, reduce variability, and uphold the highest standards of precision engineering.
Q: How does your system enable manufacturers to effectively detect and trace defects throughout the production process?
A: Our sensors do more than just monitor—they empower manufacturers to measure production in real time. Embedded directly within the CNC environment, these systems assess whether the metal is being cut precisely to design specifications—during the machining cycle itself.
This in-process measurement uncovers any deviation instantly. From there, the system can automatically send corrective data back to the CNC machine, enabling real-time adjustments without human intervention. The result? Seamless auto-corrections, executed right at the source.
Take, for example, our broken tool detectors. These systems not only check tool profiles but also detect fractures or tool wear with pinpoint accuracy. If a broken tool continues cutting, it risks scrapping the entire part—leading to costly rework and material waste. Our solution stops that loss in its tracks.
By identifying issues before they escalate, we help manufacturers eliminate rejection at the root. Every component is produced with surgical precision—right the first time. That principle underpins every Renishaw innovation. We design our solutions to deliver uncompromising quality from the very first cut.
Q: Does your system have the capability to detect structural deformities in tools or finished products?
A: To put it succinctly, you can check both the ID and OD. This process allows for precise data delivery to the machine, offering micron-level accuracy. While this provides valuable insights, it doesn’t assess material properties directly. For that, we use other solutions, such as Raman spectroscopy, which analyzes the material composition. This approach not only helps measure the tool but also enables accurate assessment of the component, providing actionable feedback.
Q: What is your perspective on the current and future market opportunities for automation tools in India?
A: Automation is undeniably the focus of the moment. Indian manufacturing is experiencing significant growth, particularly in sectors like aerospace and defense, automotive, and medical industries. The China-plus strategy, the surge in manufacturing, and the expansion of the semiconductor and electronics industries all contribute to this momentum.
As these industries expand, numerous manufacturers are stepping up to supply parts—whether small or large. In this context, ensuring quality is paramount. To achieve that, automation is essential. This is why we firmly believe automation should be accessible to all. Importantly, automation isn’t limited to robots. Even within a CNC machine, simple tools like a tool setter can facilitate automation, enhancing precision and efficiency.
This is why we advocate for equipping every CNC machine with a probe to automate processes. With such automation, manufacturers can produce high-quality parts consistently. Achieving this standard of quality is crucial for India’s growth as a manufacturing powerhouse. To successfully export, Indian manufacturers must produce parts that are defect-free and can compete on the global stage, alongside players like China and Taiwan, who lead in robot manufacturing.
In summary, automation will play a pivotal role in India’s manufacturing future. At Renishaw, we are excited about the growth prospects in the Indian market and are optimistic about the tremendous opportunities ahead.
Q: What innovations or enhancements are you planning to introduce to your existing product range over the next 5 to 10 years?
A: Our tagline, “Apply Innovation,” encapsulates who we are. We are pioneers in innovation, consistently leading the way with groundbreaking solutions. Every year, we introduce new products that push the boundaries of what’s possible.
At the recent IMTEX event, we unveiled the world’s smallest wireless probe, which fits comfortably between your two fingers. This miniature probe is designed for the smallest CNC machines, capable of producing intricate parts, such as watch components or eyeglass frames. Innovation is at the core of everything we do.
In addition to this, we launched our smart manufacturing data platform, a tool that enables manufacturers to monitor the performance of each machine in real time. It provides critical metrology data, allowing manufacturers to analyze operations and take corrective actions swiftly.
This is just the beginning. We are constantly innovating, with several new products already in the pipeline. Our advancements extend to IoT and digitalization, integrating these technologies into our solutions. For instance, our sensors provide real-time data to machines, enhancing their capabilities and performance.
Our Equator gauging system is another example of innovation—it’s an advanced, multi-gauge system that brings precision to the forefront. We are committed to advancing our product lineup further with new releases on the horizon.
While we are renowned for our expertise in machine tools and coordinate measuring machines (CMM), we also support machine tool manufacturers with machine alignment, offering calibration devices as part of our diverse product range. Our reach extends to other industries, too, including Raman spectroscopy and healthcare, showcasing our broad capabilities.
Renishaw dedicates a significant portion of its profits to research and development, underscoring our commitment to continuous improvement. This relentless focus on innovation is at the heart of our brand, which is why we proudly say: Apply Innovation.
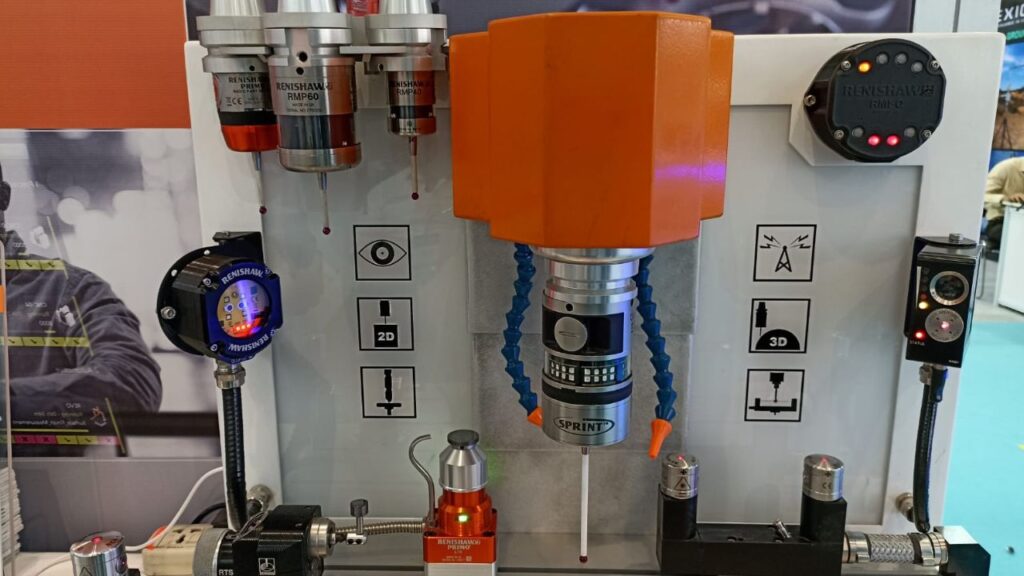