Urja Products Pvt. Ltd. has firmly established itself as a pioneer in India’s technical textiles sector, delivering advanced fiberglass and composite fabric solutions. Originally founded in 1969 as Unnati Industries and rebranded in 1989, the Ahmedabad-based company has transformed into an innovation-driven powerhouse, consistently engineering materials that exceed stringent industrial benchmarks.
Operating across two expansive manufacturing units covering 5,500 square meters and powered by a 2,000+ kW capacity, Urja runs a high-performance, agile production ecosystem. A strategic network of agents in 22 major cities reinforces its pan-India footprint, ensuring swift delivery and responsive customer service. Moreover, the company’s cutting-edge infrastructure—featuring high-speed twisting machines, automated looms, and precision-controlled coating lines—guarantees outstanding quality and process consistency.
Urja’s product portfolio is both diverse and specialized. It includes PTFE-coated fiberglass fabrics, aramid and carbon fabrics, silica textiles, welding blankets, furnace curtains, filter bags, and fabric expansion joints—solutions tailored to sectors ranging from aerospace and automotive to power generation and industrial processing.
Innovation is woven into the company’s DNA. In 1972, BHEL honored Urja with the Import Substitution Award. In 2000, the Government of India recognized the company’s development of Viton-coated glass fabrics for aircraft fuselages—an industry first. Today, Urja’s in-house R&D team continues to push boundaries, advancing high-performance textile engineering with relentless focus.
At the 5th AeroDef India Manufacturing Exhibition & Conference, Anshul Nanavaty, Managing Director of Urja Products Pvt. Ltd., shared his insights with The Interview World. He detailed Urja’s core offerings in technical textiles, spotlighted the company’s innovations in carbon fiber composite materials for avionics, and explained why these composites outperform conventional alternatives. He also emphasized their cost-effectiveness and outlined his long-term vision for innovation-led growth.
Here are the key takeaways from this compelling conversation.
Q: Can you elaborate on Urja’s core offerings in the technical textiles domain, particularly the types of carbon fiber composites you manufacture and their applications across different industries?
A: We begin by sourcing premium fibers, including aramid, glass, and carbon, known for their exceptional strength and durability. These fibers are then meticulously woven into specialized technical textiles designed to meet precise performance standards. After weaving, we apply various finishing treatments to enhance the fabric’s characteristics, such as resistance to heat, wear, or chemicals, depending on the application. The final step in the process is converting these woven fabrics into advanced composites.
Composites are lightweight yet highly robust materials that replace traditional metals in many industries. Using resins like epoxy or phenolic, these composites are essential in critical sectors such as wind energy, automotive, aerospace, and defense. From fiber to finished composite, we handle the entire manufacturing process with precision and expertise.
Q: What specific types of carbon fiber composite materials does Urja develop for the avionics sector?
A: We manufacture critical components such as radomes, aircraft and helicopter wings, and entire drone structures. These parts are crafted using advanced carbon or glass composites, which provide the necessary strength, lightweight properties, and durability.
Q: How do carbon fiber composites compare with conventional materials?
A: Carbon fiber composite products have remained irreplaceable since their invention. They continue to be the most suitable materials for industries that require strength, durability, and lightweight characteristics. While efforts are made to further reduce weight, the core material itself has remained unchanged. The industry’s reliance on carbon fiber composites is a testament to their unmatched performance and versatility.
Q: How does the affordability of your carbon fiber composite products compare to imported alternatives?
A: Since we manufacture carbon fiber composites in India, our products are more competitively priced compared to those from Europe or the United States. This local production advantage allows us to offer high-quality materials at a more cost-effective rate.
Q: Are there any long-term innovations or R&D initiatives Urja is pursuing in the technical textiles space?
A: Innovations within our industry focus on expanding the range of end products we produce. By leveraging the same high-performance fabrics, we continue to develop an increasing variety of composite products, enhancing both functionality and application.
Q: What is your long-term vision for Urja over the next five to ten years, particularly in terms of business growth?
A: Our vision for growth involves expanding far beyond our current capabilities. We are actively exploring new opportunities in the aerospace and defense sectors, with a clear focus on enhancing our presence in these high-demand industries. These two avenues represent key areas where we see significant potential for growth and innovation.
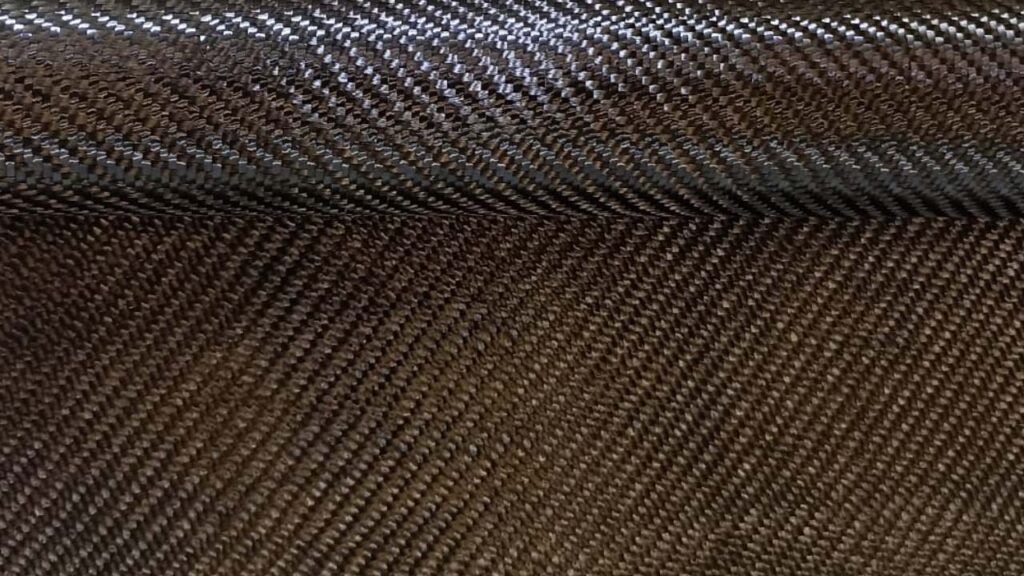