Established in 1998 and headquartered in Pune, DesignTech Systems Ltd. has emerged as a pioneering force in CAD/CAM/CAE, PLM solutions, additive manufacturing, and comprehensive engineering services. Over the last 27 years, the company has empowered more than 2,200 clients across diverse sectors, including automotive, aerospace, industrial machinery, and consumer goods.
Leveraging strategic partnerships with global technology leaders such as Altair, Stratasys, Siemens, and MathWorks, DesignTech delivers end-to-end solutions that seamlessly integrate the entire product development lifecycle—from concept and design to simulation, prototyping, and production support. Furthermore, the company actively contributes to industry upskilling through its DesignTech CAD Academy, an authorized training partner for Altair and Dassault Systèmes, ensuring a steady pipeline of skilled engineering talent.
With a dynamic team of over 750 professionals and a strong presence in more than 10 cities across India, DesignTech has also established a robust international footprint, operating offices in the USA, Singapore, Hong Kong, and Germany. Through relentless innovation and disciplined execution, the company continues to redefine the frontiers of engineering and product design.
At the 5th AeroDef India Manufacturing Exhibition & Conference, The Interview World engaged in an exclusive conversation with Ravi Patil, General Manager – Technical at DesignTech Systems Pvt. Ltd. In this interaction, he articulates the company’s core competencies in additive manufacturing, the key industries it serves, and the growing traction of this technology across sectors. He also elaborates on DesignTech’s specialized offerings for the medical field and shares insights into their focused R&D efforts aimed at advancing material innovation in additive manufacturing.
Here are the key takeaways from his compelling insights.
Q: Could you walk us through the core solutions and services in additive manufacturing that DesignTech Systems offers, and how they cater to the evolving needs of industries today?
A: At DesignTech Systems, we specialize in CAD/CAM and PLM solutions, with a strong focus on additive manufacturing. Our expertise spans the entire design spectrum. We provide advanced software tools for design creation and simulation, enabling engineers to visualize and validate their concepts with precision.
Beyond design, we offer comprehensive additive manufacturing capabilities. These include not just rapid prototyping, but also design validation, functional testing, and production of end-use parts. This allows our clients to move seamlessly from concept to final product—all within a digital framework.
What truly sets us apart is our ability to eliminate the need for traditional mass manufacturing methods such as moulding. Instead, using the same additive manufacturing technology, clients can directly print and deploy parts for end-use applications. That is the space we operate in—and it defines our core strength.
Q: Which key industries does DesignTech Systems serve with its additive manufacturing design services and solutions, and what specific needs do these solutions address?
A: When it comes to additive manufacturing, we cover the entire spectrum. From automotive and aerospace to medical—where we have a particularly strong presence—we operate across diverse domains. Our capabilities extend to white goods, civil engineering, and architectural applications. In short, name any segment, and you’ll find us there.
Q: In which sectors do you see additive manufacturing gaining the most traction, and what factors are driving its adoption there?
A: Initially, aerospace was the front-runner in adopting 3D printing, followed closely by the automotive industry. Both sectors have heavily integrated this technology into their processes. Recently, however, white goods manufacturers have begun leveraging our technology for styling purposes. At a recent event, for instance, we showcased products in various colours—demonstrating how exterior design can evolve while the interior remains constant. In today’s market, it’s the exterior design that captures customer attention, and that’s where styling becomes critical. Manufacturers use our technology to create multiple design iterations, present them to management, and select the most appealing option for market launch. Additive manufacturing plays a key role in this decision-making process.
Additionally, a new trend emerging in India is the use of 3D printing in the medical field. We’re engaging with numerous surgeons who are exploring how to incorporate this technology into medical applications.
Q: Could you elaborate on the specific additive manufacturing solutions you offer for the medical sector, and how they are addressing current challenges or improving patient outcomes?
A: In the medical field, we assist doctors in pre-planning surgeries, enhancing their ability to perform complex procedures with greater precision. To illustrate, consider a patient with a critical tumour. Rather than relying on traditional planning, we can print a detailed, 3D replica of the patient’s anatomy, including the tumour, from a DICOM image. The doctor then uses this model to simulate the entire surgery, allowing them to determine the best approach for tumour removal, minimizing blood loss, and preparing for every detail. When they step into the operating room, the real-time anatomy will match what they practiced on the table.
We provide a tactile, lifelike experience—replicating organs, bones, and skin—ensuring the doctor feels fully prepared. This process not only boosts the doctor’s confidence but also helps explain the procedure to the patient, fostering clarity on the surgery ahead. With this approach, both doctor and patient are mentally aligned, and the benefits are clear.
One of the most significant advantages we’ve observed is a reduction in surgery time—often by more than 50%. This shorter procedure time benefits everyone involved: the patient, who experiences less stress; the doctor, who can perform more surgeries; and the hospital, which increases its capacity. Furthermore, it’s not just the surgeon’s time that is reduced, but also the time of the entire surgical team, including anaesthesiologists. This creates a win-win situation for all parties involved.
Q: Given that material innovation is pivotal to the advancement of additive manufacturing, is DesignTech Systems actively engaged in R&D initiatives focused on developing or leveraging new materials?
A: I’ve been working in additive manufacturing for nearly two decades. When I first started, we focused on just one material—ABS. But today, we offer over 150 materials, and that number continues to grow each year as we invest heavily in R&D.
Our R&D efforts are driven by customer feedback and market needs. Often, customers approach us with specific material requests. Initially, our materials were designed to withstand up to 100 degrees Celsius. Today, however, we are working with materials capable of enduring more than 250 degrees, with applications that extend into space. These advanced materials even feature degassing properties, further pushing the boundaries of what’s possible in additive manufacturing.
We are committed to continuous innovation, constantly evolving based on customer demands and technological advancements.
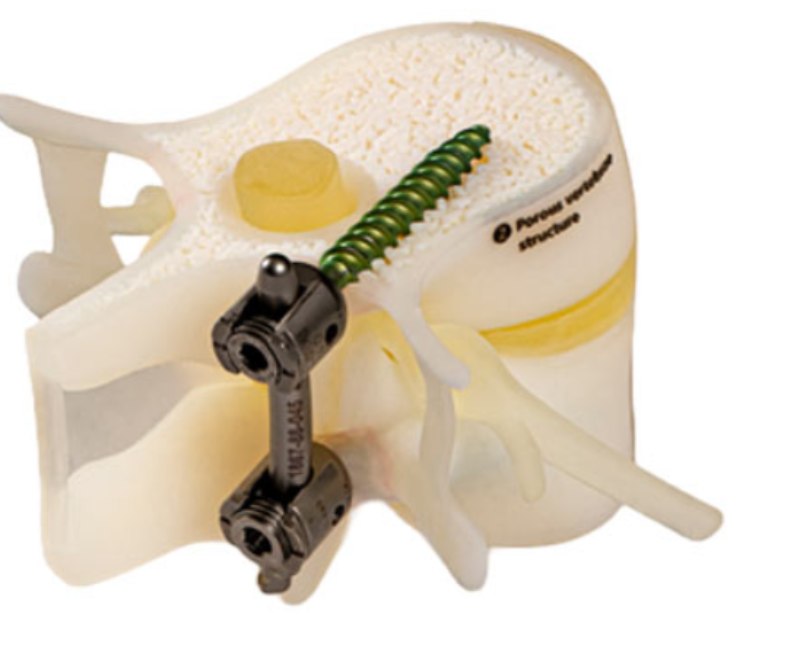