Headquartered in Jabalpur, Madhya Pradesh, Zavi Medicare LLP has rapidly emerged as a leading force in the manufacturing of single-use medical devices. The company operates advanced production facilities that include ISO 7 (Class 10,000) certified clean rooms for assembly and ISO 8 (Class 100,000) certified areas for moulding—ensuring uncompromising quality at every stage. Zavi Medicare’s diverse portfolio features I.V. cannulas, three-way stopcocks, spinal needles, endotracheal tubes, extension lines, and several other critical devices, with multiple innovative products currently in the pipeline.
Driven by ISO 13485:2016 standards and Good Manufacturing Practices (GMP), the company enforces rigorous quality control protocols. Moreover, Zavi Medicare nurtures innovation by working closely with healthcare professionals to develop medical solutions that are not only technically sound but also user-centric and accessible.
As a major employer in the Mahakoshal region, the company plays a pivotal role in stimulating local economic development. More importantly, its unwavering commitment to universal healthcare is reflected in its mission to deliver world-class medical equipment to providers across geographies.
Zavi Medicare has firmly established its presence on the global stage. With valid product registrations in countries such as Russia, Kazakhstan, Kyrgyzstan, Turkmenistan, Uzbekistan, Tajikistan, and Indonesia, the company continues to expand its international footprint. At home, it remains an active player in the Indian market, having successfully supplied products to various government organizations and public sector undertakings in the past year.
In an exclusive conversation with The Interview World, Vivek Goswami, Founder and CEO of Zavi Medicare LLP, outlines the company’s flagship products, showcases the cutting-edge automation technologies embedded in its manufacturing lines, and evaluates the rising global appetite for Indian-made medical devices. He also sheds light on the evolving dynamics of the global medical industry and emphasizes the urgent policy interventions required to position India as a global hub for medical equipment manufacturing.
Here are the most compelling insights from his powerful interview.
Q: Could you highlight the key products that Zavi Medicare offers in the healthcare sector?
A: Zavi Medicare officially commenced operations in 2022 after securing a valid license from the Ministry of Health, Bhopal. Since then, we have focused exclusively on manufacturing single-use disposable medical products—a vast and critical segment within the healthcare industry.
Our journey began with the launch of our flagship product, the Intravenous (IV) Cannula. From the outset, our mission has been clear: to deliver superior-quality medical devices at globally competitive prices—not just for India, but for healthcare markets worldwide.
Today, we produce approximately 150,000 IV cannulas each day. With growing demand and enhanced capacity, we are firmly on track to scale production to 200,000 units daily by August 31st. This goal reflects both our operational agility and our commitment to expanding access to essential medical supplies.
At the same time, we are actively developing three additional products: the Three-Way Stopcock, Extension Line, and Spinal Needle. We anticipate that at least two of these will be market-ready and launched alongside our IV Cannula line by the end of August.
With every step, we remain focused on quality, innovation, and affordability—cornerstones that define Zavi Medicare’s growing impact on the global healthcare landscape.
Q: With automation becoming a key trend in medical manufacturing, what types of advanced equipment and technologies are being utilized in your production facilities to enhance efficiency and quality?
A: Despite India’s abundant labor force, labor shortages have become a growing concern in major metropolitan areas. This challenge has prompted a widespread industry shift toward automation, especially among both emerging players like us and established companies with decades of experience.
At Zavi Medicare, we have embraced this transformation by integrating automation into our manufacturing process. While we initially began with semi-automatic machinery—given the capital constraints typical of any new venture—we always envisioned a gradual move toward full automation. Investing immediately in million-dollar systems wasn’t feasible during our early stage. However, as we built our market presence and gained traction, we took decisive steps to scale up.
Today, our production line features a mix of semi-automated systems and two fully automatic, human-touch-free machines dedicated to manufacturing IV Cannulas. These state-of-the-art machines significantly enhance precision, consistency, and hygiene, setting a new benchmark for quality in our product line.
Importantly, we have committed ourselves to the ‘Make in India‘ vision. Inspired by our Honorable Prime Minister and supported by national policy, we prioritize indigenous technologies. Rather than relying on foreign imports, we source and deploy machines manufactured in India—many of which are built in collaboration with global leaders like Toshiba and Shibaura from Japan.
As a result, our manufacturing infrastructure is now powered by a robust combination of Japanese-engineered precision and Indian manufacturing strength. This synergy not only reinforces our commitment to self-reliance but also positions Zavi Medicare as a forward-looking, innovation-driven company aligned with India’s industrial resurgence.
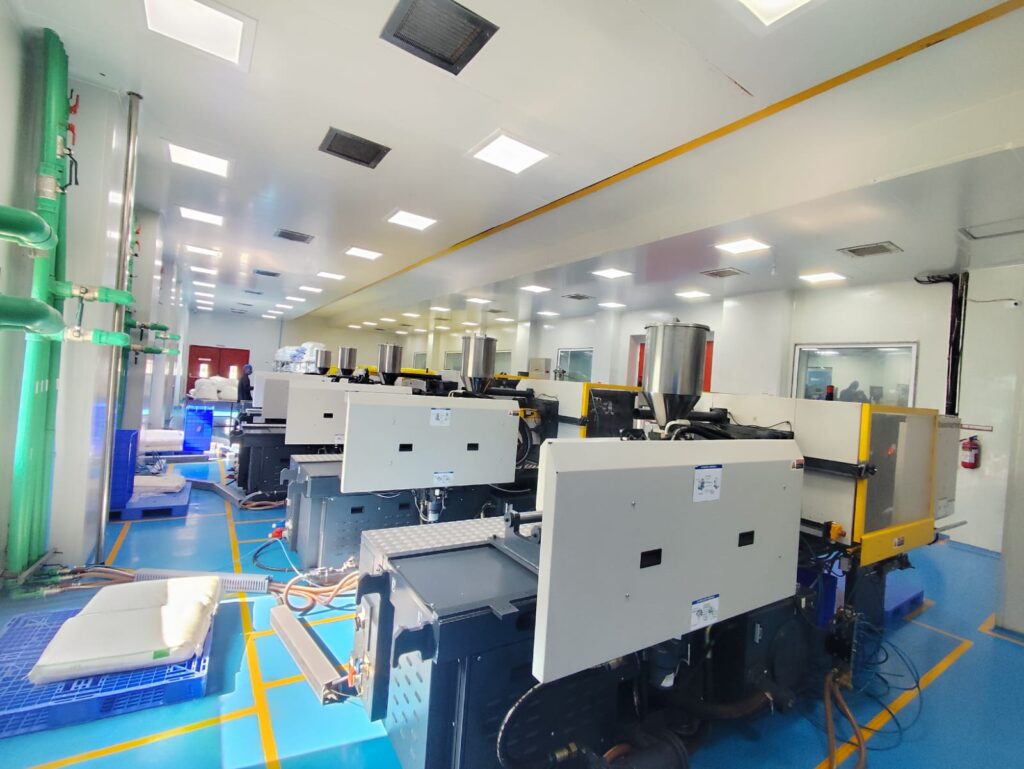
Q: How do you assess the global demand for Indian-manufactured medical equipment and products, and which markets are showing the most promising growth opportunities?
A: I’ve spent a significant part of my life in this state, witnessing its evolution firsthand. Back in the 1990s and early 2000s, China clearly led the way in the medical disposables sector. India, however, maintained a strong position in pharmaceuticals then—and continues to do so today.
That said, the landscape has shifted dramatically since 2010. Indian manufacturers have made remarkable strides, particularly in the domain of single-use medical disposables. Whether in cardiology, orthopedics, or basic items like infusion and transfusion sets, we’ve seen substantial innovation and quality enhancement.
With strong backing from the current government, manufacturers now feel confident in their ability to surpass China in this space. In fact, in several product categories, we’ve already outpaced not just Chinese competitors but even some European counterparts. India benefits from not only cost-effective labor but also a large, skilled workforce. Moreover, we operate with the same advanced equipment used in top European facilities, ensuring our output meets global standards.
As a result, Indian-made medical disposables are now widely accepted across international markets. Take our own company, for example—despite being relatively new, we are already exporting directly to nine countries.
This growth trajectory is undeniable. The future of India in the medical disposables industry is not just promising—it is exceptionally bright.
Q: Post-COVID, what significant shifts have you observed in the global medical landscape, particularly in the Indian medical manufacturing sector?
A: Before COVID-19, most countries relied heavily on Chinese and Indian manufacturers, with some dependence on European suppliers as well. However, the pandemic exposed a critical vulnerability. Nations with smaller populations struggled to produce high-volume essential items such as syringes, airframes, and COVID test kits. As a result, they turned to imports—primarily from China, India, and a few others.
Since then, global policy landscapes have shifted. Many governments are now pushing domestic manufacturers to localize production and reduce import dependency. Yet, despite this shift, one trend stands out: global trust in Indian suppliers has grown significantly—surpassing even that of our neighbor, China.
India’s decisive support to other nations during the pandemic played a pivotal role in earning this trust. Today, that goodwill has translated into long-term strategic partnerships. Across the world, India is increasingly recognized as a reliable, scalable, and quality-driven manufacturing hub for medical disposables.
Importers no longer perceive Indian products as inferior. Instead, they see quality, consistency, affordability, and above all—dependability. As a result, Indian manufacturers are now gaining unprecedented access to global markets. This level of international acceptance and recognition was unthinkable a few years ago.
Simply put, India has emerged not just as a manufacturer, but as a preferred global partner in the medical disposables sector.
Q: What policy measures do you believe are essential to strengthen medical equipment manufacturing in India, and what specific steps should the government take to support the industry?
A: Any reform in the medical devices sector is welcomed by most manufacturers. However, I firmly believe we must adopt a more liberal approach toward export policies. India earns valuable foreign exchange through medical exports—yet, exporters often receive minimal support. We urgently need greater incentives for exporters to remain competitive on the global stage.
Equally important, we must streamline the bureaucratic hurdles that delay operations. Securing clearances—whether for fire safety, pollution control, or manufacturing licenses—continues to be a time-consuming and inconsistent process. While some state governments have made commendable progress, widespread inefficiencies persist.
This needs urgent attention. Manufacturers invest their hard-earned savings, secure loans by pledging personal assets, and assume significant financial risks. The least they deserve is institutional support and a system that enables—not obstructs—growth.
For instance, the cost of capital remains prohibitively high. Loans at 9–10% interest are unsustainable for manufacturers in their early stages. The government must intervene to make credit more affordable and accessible.
Additionally, regulatory procedures—especially for critical licenses—must be simplified and time-bound. Beyond this, India must offer substantial export incentives, at least for the first three to four years, to help manufacturers establish a foothold in international markets.
State governments also have a crucial role to play. They should prioritize purchasing from local manufacturers to promote regional self-reliance. Unfortunately, many states, such as Madhya Pradesh, still refuse to procure from local firms unless they have a proven track record of three years. But how can a new manufacturer survive three years without any institutional orders or support?
I’ve survived that phase—but many won’t. The hurdles are simply too high. It’s time state governments like MP and UP take bold steps to support emerging manufacturers. If local companies are left to struggle alone, the very spirit of ‘Make in India’ stands compromised.
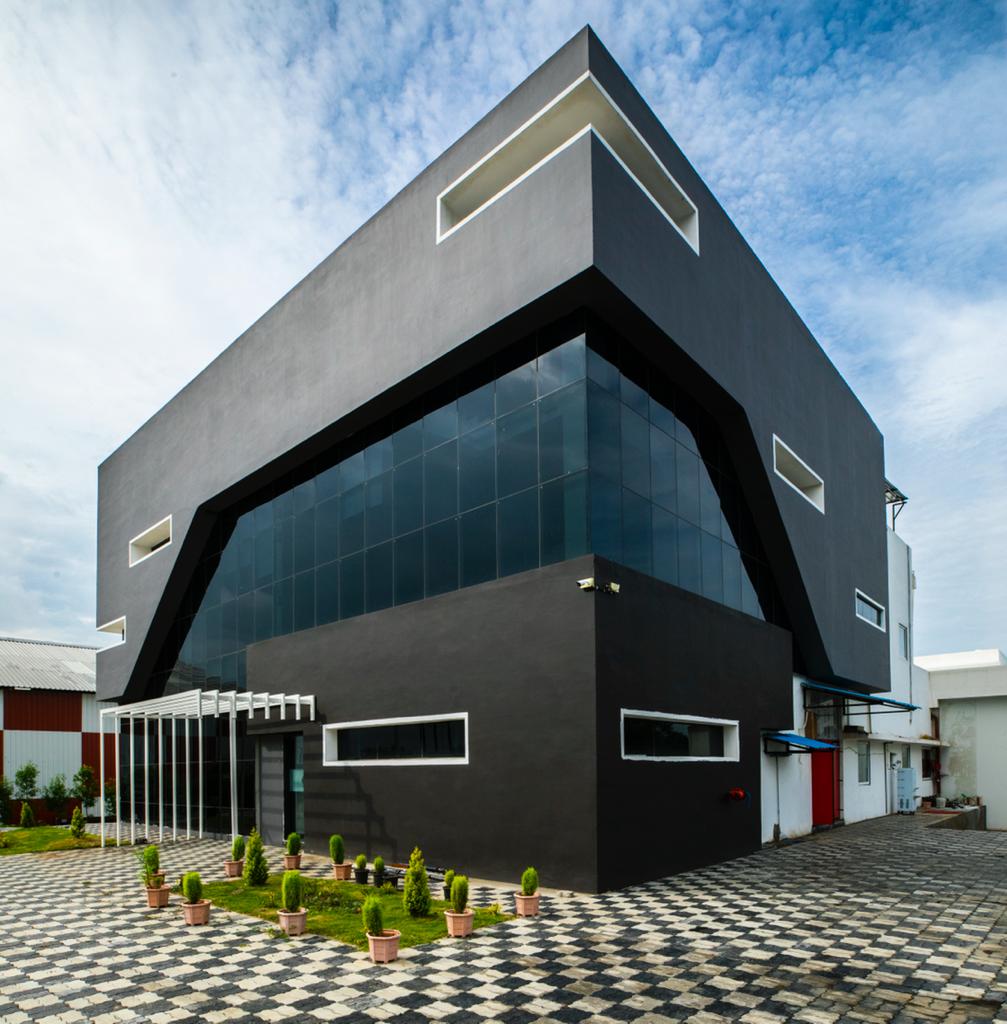